Case
froth flotation process for nickel
2020-07-13T23:07:23+00:00
NICKEL AND COBALT ORES: FLOTATION
Figure 5 Flotation selectivity in the separation of pentlandite from pyrrhotite using sulfur dioxide and diethylenetriamine with sodium isobutyl xanthate (pH+92, 25 g t 1 Dow froth!250) (Reprinted with permissionfrom the CanadianInstitute of Mining, Metallurgy and Petroleum) Figure 6 Flotation results obtained with Clarabelle ore fromKeywords: flotation, process optimization, Taguchi orthogonal array, ANOVA 1 Introduction Froth flotation is widely used for separating base metal sulphide minerals in complex ores One of the major challenges faced by the flotation of these ores is the ever varying grade and mineralogy as the ore is exploited (Kabuda et al, 2011) As in Flotation of NickelCopper Sulphide Ore: Optimisation of froth flotation process in case of nickel extraction Floatation SlideShare Jan 30, ;32;Oil and froth float on the surface along with the sulphide ore The gangue particles being insoluble in oil remain at the bottom of the water tank The froth is removed and allowed to settle down This is called the frothfloating process This process is used for sulphide ores of Cu, Pb and Zn 10 froth flotation process in case of nickel extraction 】

Optimising froth condition and recovery for a nickel ore
1/11/2008 Froth flotation Flotation kinetics Modelling Sulphide ores Process optimisation 1 Introduction For simple empirical flotation models it is typically easy to generate the necessary data from test work and circuit surveys Models of this type can accurately predict recovery and grade by measuring particle floatability in a laboratory cell and translate this into an industrial scale by 2/5/2010 The video shows froth zone loaded with sulphides in batch flotation of Ultramafic Nickel Ore after grinding and aging Aging was used to allow some time to form elemental sulphur films on sulphideCollectorless Froth Flotation of Ultramafic Nickel Ore For example, in the process of coppernickel mixed flotation, the pH value is adjusted to obtain the maximum possible recovery rate In the mixing and dosing process, the pulp with suitable concentration should be prepared for the next process When the adjusted slurry is sent to the flotation tank, the ore particles with strong surface hydrophobicity adhere to the surface of the bubble, and Common Questions About Froth Flotation Process Technology

Nickel: smelting, producingMetalpedia
In hydrometallurgical processes, nickel sulfide ores undergo flotation (differential flotation if Ni/Fe ratio is too low) and then smelted After producing the nickel matte, further processing is done via the SherrittGordon process First, copper is removed by adding hydrogen sulfide, leaving a concentrate of only cobalt and nickelA process for the beneficiation of nickel bearing laterite ores by means of froth flotation wherein a dispersed pulp of the ore is conditioned with a fatty acid type collecting agent either at an elevated pH to produce, following flotation, an enriched flotation tailing or at a reduced pH to produce, following flotation, an enriched flotation concentrateFLOTATION OF LATERITIC NICKEL ORES WESTON D,CA15/6/2017 Table of ContentsRaw OrePit Ore SampleShaft Ore SampleLaboratory Copper Nickel Ore Flotation Pit Sample ProcedureResultsShaft SampleBatch Copper Nickel Flotation Copper Nickel Flotation
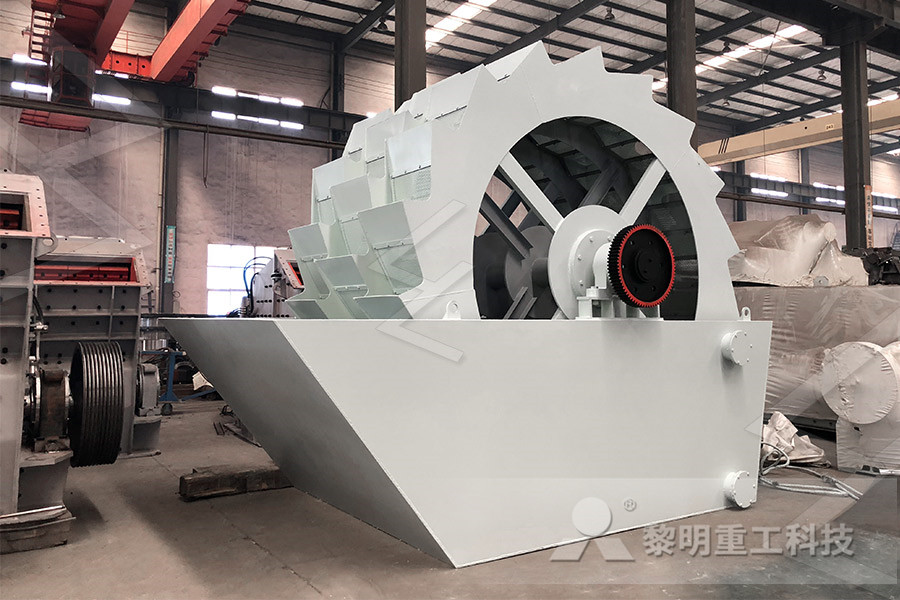
Optimising froth condition and recovery for a nickel ore
1/11/2008 Froth flotation Flotation kinetics Modelling Sulphide ores Process optimisation 1 Introduction For simple empirical flotation models it is typically easy to generate the necessary data from test work and circuit surveys Models of this type can accurately predict recovery and grade by measuring particle floatability in a laboratory cell and translate this into an industrial scale by An experiment of Froth Flotation was carried out on a NickelCopper Sulphide ore in order to extract the Copper and nickel mineral from the material The main aim of this experiment was to (PDF) FROTH FLOTATIONThe froth flotation process mainly includes grinding, slurry adding, froth flotation separation and dehydration of foam products and tailing products after froth flotation Before the flotation operation, the ore needs to be ground to an optional size range by the grinding mill, generally less than 01 mon Questions About Froth Flotation Process Technology

(PDF) Sulphidization to improve the nickel oxide recovery
Sulphidization was conducted before froth flotation to convert the surface of nickel oxide to nickel sulphide Key variables considered were type of sulphidization reagent, sulphidization Eh, timeThe pyrrhotite is then sent to froth flotation cells, and produces a 3% nickel concentrate The non magnetic ore is sent to a series of rougher, cleaner flotation cells, and produces a 31% copper concentrate The tailings from these cells is sent to another flotation cell, to recover the nickel, and the concentrate is combined with the 3% nickel concentrate to produce a 12% nickel concentrate Processing Nickel Ores mineengineer1 Froth Flotation – Fundamental Principles Froth flotation is a highly versatile method for physically separating particles based on differences in the ability of air bubbles to selectively adhere to specific mineral surfaces in a mineral/water slurry The particles with attached air bubbles are then carried to the surface and removed, while the particles that remain completely wetted stay 1 Froth Flotation – Fundamental Principles

Minerals Processing in Mining: Getting stability in your
7/11/2013 Most flotation cells comprise of a pulp and froth phase The froth phase is used primarily for three functions: 1 to create an environment for floated particles to separate from the bulk slurry;Froth flotation process mainly includes grinding, pulp conditioning and dosing, froth flotation separation and dewatering of foam products and tailings products after flotation Before the froth flotation operation started, the ore needs to be ground to optional particle size range Generally it is 3 Factors Affect Froth Flotation Process? MiningpediaThe new StackCell™ flotation technology was developed to specifically target this particle size range, and was tested at pilot plant scale at Mt Keith Nickel Concentrator The streams tested, Slimes Rougher Tailings and Fines/Slimes Cleaner Tailings, represent 21% The Application of High Intensity Flotation Technology at
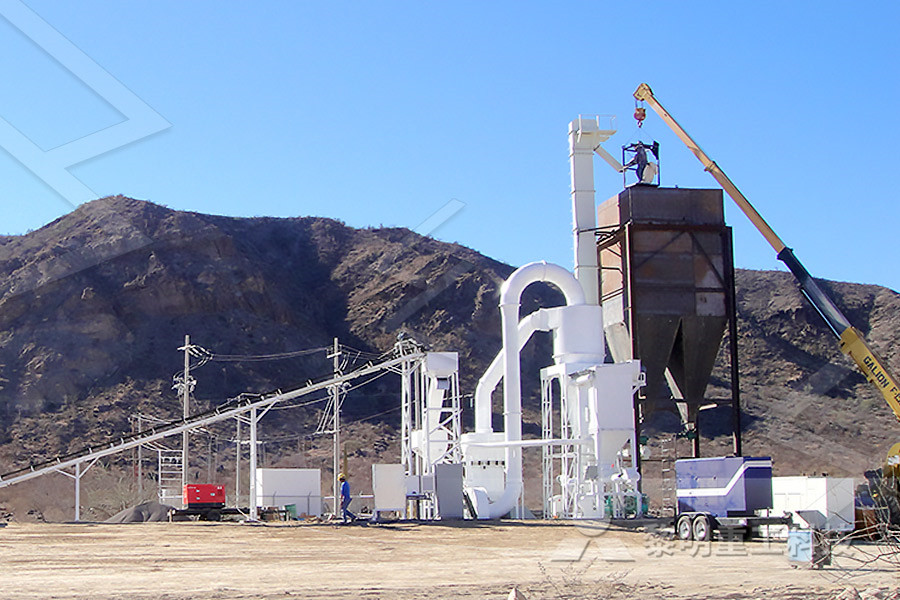
Flotation SlideShare
27/7/2015 Flotation 1 Perth Brisbane Melbourne Noosa L 6, 524 Hay St Perth WA 6000 P: (+61 8) 9421 9000 PO Box 5778 St Georges Tce WA 6831 U 4,14 Merivale St South Brisbane QLD 4101 P: (+61 7) 3029 6220 117 Miller St Thornbury VIC 3071 P: (+61 3) 9495 2666 ABN 66 009 357 171 E: info@metsengineering W: metsengineering Presented by Peter Steckis Consulting 1/11/2008 Froth flotation Flotation kinetics Modelling Sulphide ores Process optimisation 1 Introduction For simple empirical flotation models it is typically easy to generate the necessary data from test work and circuit surveys Models of this type can accurately predict recovery and grade by measuring particle floatability in a laboratory cell and translate this into an industrial scale by Optimising froth condition and recovery for a nickel ore The froth flotation process mainly includes grinding, slurry adding, froth flotation separation and dehydration of foam products and tailing products after froth flotation Before the flotation operation, the ore needs to be ground to an optional size range by the grinding mill, generally less than 01 mon Questions About Froth Flotation Process Technology

Processing Nickel Ores mineengineer
The non magnetic ore is sent to a series of rougher, cleaner flotation cells, and produces a 31% copper concentrate The tailings from these cells is sent to another flotation cell, to recover the nickel, and the concentrate is combined with the 3% nickel concentrate to produce a 12% nickel concentrateThe preferential froth flotation process refers to float a kind of mineral first and inhibit another kind of mineral when the polymetallic mineral contains two or more kinds of useful components, and then activate and float other kinds of mineral This process that recycles the useful minerals in turn is the preferential froth flotation processSeven Common Froth Flotation Processes Xinhai7/11/2013 The amount of froth crowding at the top of a flotation cell determines the amount of froth surface area for a given flotation cell During the project design phase, the optimum amount of froth Minerals Processing in Mining: Getting stability in your

Differences and Applications of Magnetic Separation and
22/12/2020 The principle behind froth flotation process is that sulphide ores are preferentially wetted by pine oil whereas gangue articles are wetted by water In this process, the suspension of a powdered ore is made with water Collectors like pine oil, fatty acids and xanthate are added to itFroth flotation is a method of separating minerals from impurities or one mineral from another The unpurified ore powder is mixed with water and reagent The reagent preferentially binds to the target ore and changes its surface characteristicsThe Application Of Froth Pump In Flotation Process 14/9/2011 Froth flotation is a three phase separation process for complex ores based on the manipulation of the difference in hydrophobicity of the solids Suspended, hydrophobic metalrich particles are contacted with, and subsequently combine to, air bubbles — whilst the more hydrophilic gangue particles sink and are recovered to the tails streamA review of froth flotation control ScienceDirect

Nickel Ore Processing Rougher Flotation
The froth flotation process was patented by E LSulman, H F K Pickard, and John Ballot in 1906, 19 years after the first cyanide process patents of MacArthur and the Forests Mineral Processing Flotation Machine Nickel nickel processing flotation equipment Jaw Crushertypes of jaw crusher,jaw crusher manufacturer,jaw crusher ma nickel 27/7/2015 Flotation 1 Perth Brisbane Melbourne Noosa L 6, 524 Hay St Perth WA 6000 P: (+61 8) 9421 9000 PO Box 5778 St Georges Tce WA 6831 U 4,14 Merivale St South Brisbane QLD 4101 P: (+61 7) 3029 6220 117 Miller St Thornbury VIC 3071 P: (+61 3) 9495 2666 ABN 66 009 357 171 E: info@metsengineering W: metsengineering Presented by Peter Steckis Consulting Flotation SlideShare