Case
iron ore pellet making process
2020-11-19T12:11:45+00:00
Iron Ore Pelletizing Process: An Overview IntechOpen
10/7/2017 Bentonite, an inorganic binder, has been the main binder used in the iron ore pelletizing process since the beginning of pellet production in the 1950s Bentonite Bentonite is an effective, widely used binder in the iron ore pelletizing process Its low price is an important factor for its extensive use However, bentonite incorporates silica and alumina, which are undesirable contaminants to pellets Additionally, it is a natural material with variable composition depending on its origin Obtaining a suitable binding effect requires a relatively large Iron Ore Pelletizing Process: An Overview26/11/2014 For the pelletizing of iron ore there are two main types of processes namely, the straight travelling grate (STG) process and the grate kiln (GK) process In the STG process, a stationary bed of pellets is transported on an endless travelling grate Iron Ore Pellets and Pelletization Process – IspatGuru

The Iron Pelletizing Process: Part One :: Total Materia
The pelletizing process is a process which contains numerous subprocesses, or process segments On the way from the mine to a final product, the iron ore goes through the following main process segments: 1) The iron ore is crushed and the waste rock is removed About 85 % of the particles should be less than 44 μm (in length, width, or height)9/11/2020 Bentonite is an effective, widely used binder in the iron ore pelletizing process Its low price is an important factor for its extensive use However, bentonite incorporates silica and alumina (PDF) Iron Ore Pelletizing Process: An OverviewNo losses in handling iron ore as pellets will not break during transport or handling 9 TYPES OF PELLETISATION PROCESS 1 Grate kiln process 2 Travelling grate process Choice of one over the other will be based more on economics rather than the technical aspects 10 GRATE KILN PROCESS Process adopts three equipment viz grate, rotary kiln and annular cooler Green balls are first dried SINTERING AND PELLETISATION OF INDIAN IRON ORES

Reduction of Iron Ore Pellets, Sinter, and Lump Ore under
23/3/2020 A blast furnace (BF) is the most common process for hot metal production in the world The BF is charged with metallurgical coke and iron‐bearing materials separately, which leads to a layered structure The iron‐bearing materials consist of iron ore pellets, lump ore, and sinter When the charge material descends, it is reduced by CO and H 223/3/2020 A blast furnace (BF) is the dominant process for making iron in the world The BF is charged with metallurgical coke and iron burden materials including iron ore pellets, sinter, and lump ore While descending in the BF the charge materials reduce The iron‐bearing materials should reduce fast and remain in the solid form until as high a Reduction of Iron Ore Pellets, Sinter, and Lump Ore under Bentonite is an effective, widely used binder in the iron ore pelletizing process Its low price is an important factor for its extensive use However, bentonite incorporates silica and alumina, which are undesirable contaminants to pellets Additionally, it is a natural material with variable composition depending on its origin Obtaining a suitable binding effect requires a relatively large Iron Ore Pelletizing Process: An Overview
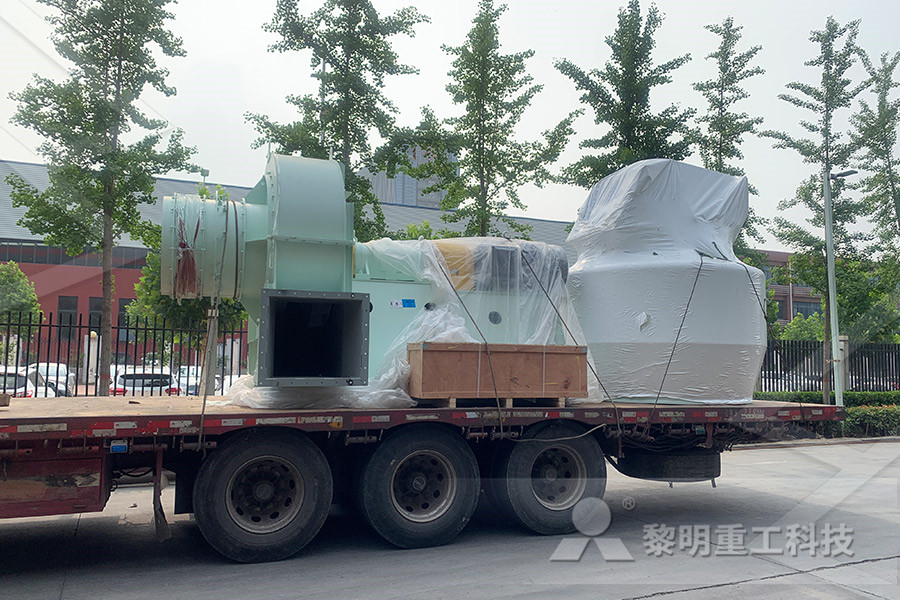
Pellet (Iron ore) Mining Fundamentals
Iron ore pellets are marblesized balls of iron ore that are fused with clay for transportation and used in steel manufacture The process of making pellets from iron ore is called pelletizing The manufacture of steel from lowgrade iron ore involves processes like mining, crushing, separating, concentrating, mixing, pelletizing, and shipping1 Pellet Process Uses and Exposures prepared by Corus Staal May 2010 Pellet Process Uses and Exposures 1 The mixture of iron bearing materials (iron ore rubble, sinter and/or pellets) and additives (flux material) are known collectively as the "burden" The burden and the accompanying coke are charged into the top of the furnace either via skips or mechanical conveyor belts It Pellet Process Uses and Exposures May 2010The formation of raw iron ore pellets, also known as pelletizing, has the objective of producing pellets in an appropriate band of sizes and with mechanical properties high usefulness during the stresses of transference, transport, and use Both mechanical force and thermal processes are used to produce the correct pellet propertiesPelletizing Wikipedia
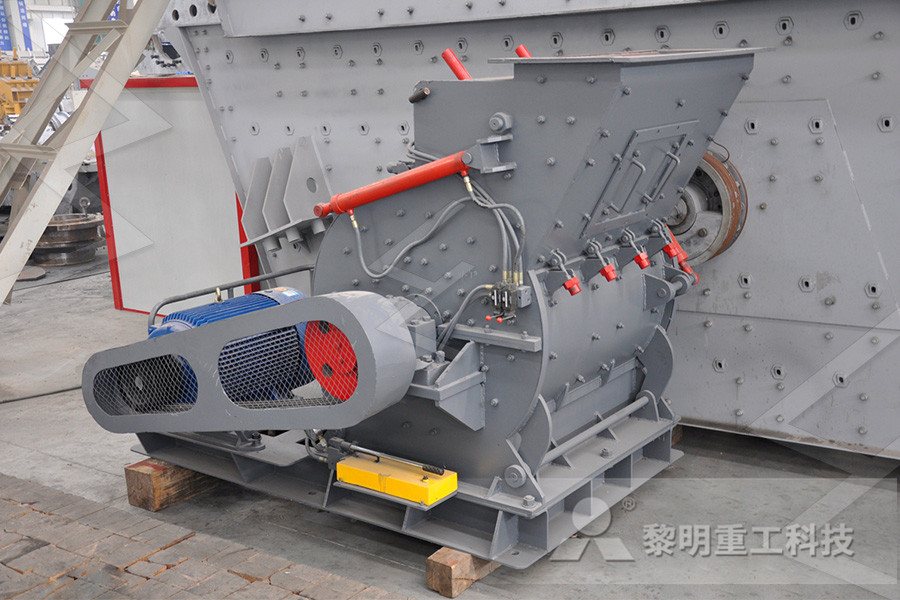
SINTERING AND PELLETISATION OF INDIAN IRON ORES
No losses in handling iron ore as pellets will not break during transport or handling 9 TYPES OF PELLETISATION PROCESS 1 Grate kiln process 2 Travelling grate process Choice of one over the other will be based more on economics rather than the technical aspects 10 GRATE KILN PROCESS Process adopts three equipment viz grate, rotary kiln and annular cooler Green balls are first dried Vale is the world’s biggest producer of iron ore and pellets, raw materials essential to the manufacture of steel Iron ore is found in nature in the form of rocks, mixed with other elements By means of various industrial processes incorporating cuttingedge technology, iron Iron Ore and Pellets Vale22/2/2021 The process is considered more efficient than making use of iron ore powder, which does not allow the hot air to freely circulate and warm the ore to a uniform temperature For this reason, the pellets are often preferable to fine iron ore products, since the ability to achieve that balance in temperature is somewhat limited with the fine ore productsWhat Are Iron Ore Pellets?

ROLE OF IRON ORE PELLETS TO ACHIEVE TARGET OF PRODUCING
Ceramic balls Green pellets Pellet movement on Disc Step 1:Production of green balls in a disc/drum where fine grained iron ore with proper size distribution and mixed with a binder (usually bentonite) and additives such as limestone/dolomite and coke fines with additional water23/3/2020 Abstract A blast furnace (BF) is the dominant process for making iron in the world The BF is charged with metallurgical coke and iron burden materials including iron ore pellets, sinter, and lump ore While descending in the BF the charge materials reduceReduction of Iron Ore Pellets, Sinter, and Lump Ore under Iron Mining Process From blasting to crushing to separation – more than 85% of the iron mined in the United States is mined in northeastern Minnesota to make our nation’s steel Blasting Taconite is a very hard rock Using explosives, the taconite is blasted into small pieces Transportation The taconite pieces are scooped up by electric shovels Each shovel can hold up to 85 tons of rock Iron Mining Process Minnesota Iron

(PDF) Iron ore pelletization ResearchGate
purities, the finer size distribution of concentrates limits their usage in iron ore sintering Therefore, pelletizing is needed to produce fired pellets from concentrates as burden materials forIron ore pelletizing, or balling, is the process of transforming fines into spherical granules anywhere from 8 – 16mm in size via tumblegrowth (agitation) agglomeration using either a disc pelletizer (pan granulator) or rotary drum Why Demand for Pelletizing is Going UpIron Ore Pelletizing Essential in Meeting Future Steel NeedsNo losses in handling iron ore as pellets will not break during transport or handling 9 TYPES OF PELLETISATION PROCESS 1 Grate kiln process 2 Travelling grate process Choice of one over the other will be based more on economics rather than the technical aspects 10 GRATE KILN PROCESS Process adopts three equipment viz grate, rotary kiln and annular cooler Green balls are first dried SINTERING AND PELLETISATION OF INDIAN IRON ORES
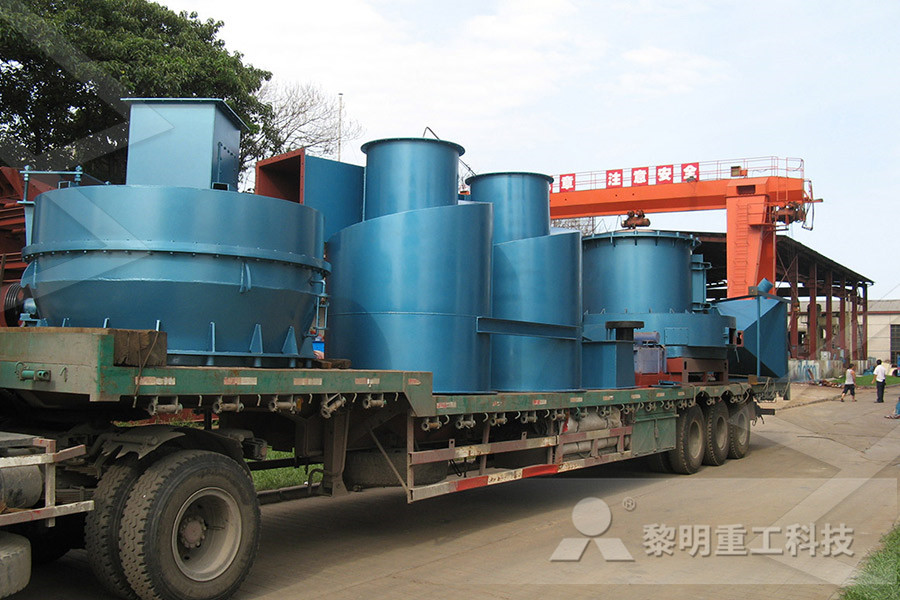
Future Process And Design Aspects In Iron Ore Pelletizing
The present situation in the field of iron ore pelletizing is briefly described with particular view of the Lurgi/Dravo travelling grate process To meet todays pellet quality requirements with regard to physical and metal lurgical properties it is often necessary to add basic fluxing materialsThe landing page presents SCARABAEUS ® 7500 pelletizing discs used for agglomerating iron ore concentrates into pellets with very tight particle size distribution (target size of 10 to 14 mm) and supporting DRIProcess (processing method for sustainable and efficient production of iron ore): “It is the direct iron ore reduction process, enabled by those uniform size pellets, which finally leads to the Sustainable and efficient production of iron ore pellets Iron / DRI Steel Making Iron ore Pellets: Fe: 640% SiO 2: 30% Al 2 O 3: 27% LOI ~ NIL Pellets in Iron Steel Making –Process Flow Pellet Industry in India • Started in 1960sMandovi pellet plants in Goa • Kudremukh (KIOCL ) 3MTPA plant in Mangalore 1987 • Tata Steel pellet plant 1980 s : 6MTPA plant • Govt Policies gave a big fillip to pellet Industry : • FM Budget speech ROLE OF IRON ORE PELLETS TO ACHIEVE TARGET OF PRODUCING

Process of sustainable and efficient production of iron
10/6/2020 Process of sustainable and efficient production of iron ore pellets Join us and Dr Jan Paul Lampke, Head of Sales Projects, Haver Engineering Gmbh, for a live webinar on Monday, 15th June at 03:00 PM (IST), 5:30 PM (Singapore time), 1:30 PM (Dubai Time), as he explains how SCARABAEUS® pelletizing discs can be used for sustainable and efficient production of iron ore pellets Iron Ore Pelletization is an agglomeration process of the disintegrated Iron Ore fines into Iron ore Pellet which is suitable for the utilization of downstream process of Iron Making The GPIL Process is the Ore ground to the required fineness through wet grinding process mainly by Ball Mills and the slurry is dewatered by pressure filtration to produce the Iron Ore ConcentrateThe Iron Ore Pellets HIRA Godawari Power Ispat Limited23/3/2020 Abstract A blast furnace (BF) is the dominant process for making iron in the world The BF is charged with metallurgical coke and iron burden materials including iron ore pellets, sinter, and lump ore While descending in the BF the charge materials reduceReduction of Iron Ore Pellets, Sinter, and Lump Ore under

Iron processing Ores Britannica
In the travelinggrate process, pellets are charged at one end and dried, preheated, fired, and cooled as they are carried through successive sections of the equipment before exiting at the other end Traveling grates and gratekilns have similar capacities, and up to five million tons of